MIM
What Is MIM?
Process Overview
When to Use MIM
General Guidelines
Technology Comparisons
Materials Range
Materials List
Design Guidelines
Designing for Manufacturability
Uniform Wall Thickness
Thickness Transition
Coring Holes
Draft
Ribs and Webs
Fillets and Radii
Threads
Holes and Slots
Undercuts
Gating
Parting Lines
Decorative Features
Sintering Support
Secondary Operations
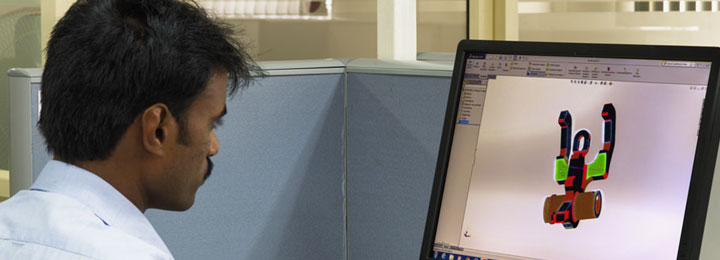
Technology Comparisons
There is a place for each of the traditional metal-forming processes: each has its own strong suits as well as its limitations. But wherever a component fabrication choice exists between MIM and one or more of the other processes, it pays to see how they stack up in a head-to-head comparison.
The following table shows how the four major processes fare in some of the more important parameters to consider.
Parameter |
MIM |
CONVENTIONAL PM |
MACHINING |
INVESTMENT |
Density | 98% |
88% |
100% |
98% |
Tensile Strength | High |
Low |
High |
High |
Elongation | High |
Low |
High |
High |
Hardness | High |
Low |
High |
High |
Complexity | High |
Low |
High |
Medium |
Surface Finish | High |
Medium |
High |
Medium |
Production Volumes | High |
High |
Low |
Medium |
Range of Materials | High |
High |
High |
Medium-High |
Cost | Medium |
Low |
High |
Medium |
MIM vs. Conventional PM
MIM can produce geometries that eliminate secondary operations
MIM offers superior density, corrosion performance, strength, ductility
MIM can combine two or more PM components into one, reducing part count
MIM parts offer superior magnetic performance
MIM vs. Machining
MIM designs save material and weight MIM provides cost savings through better material utilization—sprues and runners can be reground and reused as feedstock with no compromise to final properties Molding from a single tool eliminates multiple set-up operations Difficult-to-machine materials can be molded into a net shape
MIM vs. Investment Casting
MIM can produce thinner wall sections, sharper cutting points MIM produces better surface finish MIM is better for small-diameter blind and through holes MIM greatly reduces requirements for finish machining MIM produces high volumes of small components at a lower cost, faster lead times